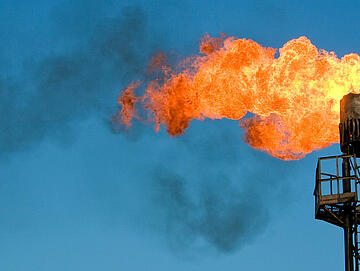
Task
- Monitoring of product quality
- Determination of important elements in raw materials, intermediates and end products
- Ultratrace analysis of nitrogen, sulfur and chlorine
Solution
- Elementary Analyzer multi EA 5000 ®
Advantages
- Analysis of viscous and solid substances
- Analysis of gases and liquefied gases
- Low-maintenance detectors from the ppb to % range
- Self Check System for optimum operational safety
An analyzer to monitor product quality
High standards apply at Dow in product and process quality, occupational safety and environmental protection. In order to meet these requirements, Analytik Jena contributes high-precision analytical measurement technology. Both in the monitoring of product quality and the control of environmentally relevant parameters, the analyzers from Analytik Jena in the laboratory ensure the necessary safety and compliance with the limit values.
These include the versatile multi EA 5000 ® elemental analyzer, which Dow uses primarily to determine important elements in raw materials, intermediates and end products to control the quality of these materials. Important tasks at Dow include sulfur analysis in petroleum derivatives. The combustion of these products produces sulfur and nitrogen oxides, which contribute to the formation of acid rain, which not only damages forests, but also poses health risks. Therefore, strict guidelines apply to the permissible exposure to sulfur compounds. Dow ensures their compliance as well as the quality of other products with the help of the analyses of the multi EA 5000 ® .
Competitive advantages of the customer
Even higher quality requirements can meet best detection limits Residue-free combustion without soot formation and contamination of the system Time and money savings Ultratrace analysis Change between vertical and horizontal combustion mode in a matter of minutes.
Two furnace modes in one analyzer
In the multi EA 5000 ® the sample is first pyrolyzed in a two-phase digestion process under a protective gas atmosphere and then oxidized at about 1000 °C in the oxygen stream. All contained sulfur, nitrogen and carbon compounds are converted into their gaseous oxides (SO 2 , NO x , CO 2 ==References== These are then detected and quantified with individual selective detectors. UVfluorescence, chemiluminescence and infrared measurement are used. If halogen compounds are contained in the sample to be examined, they are converted into gaseous hydrogen halides (e.B. HCl) in the combustion process. These are transferred to a measuring cell in which a titration process takes place.
The multi EA 5000 ® oxidizes all types of samples in a high-temperature furnace in a targeted and controlled manner. The double-furnace concept allows the laboratory team to choose between vertical and horizontal combustion modes, depending on the sample matrix and analysis target. The conversion is done in a few simple steps. A conventional elemental analyzer does not offer this analytical convenience.
In horizontal mode, the sample is inserted fully automatically and in a controlled manner into the combustion part. This is ensured by flame sensor technology. "Each sample is burned completely and residue-free. This is the best prerequisite for reliable measurement results. At the same time, we save a lot of time in method development, because thanks to the flame sensor, each sample can be oxidized quickly and easily in variable quantities without precise knowledge of its combustion characteristics," says Peter Frenzel, Head of Analytics and Quality Manager at Dow. In vertical furnace mode, the lowest element concentrations are best determined. In the ultratrace analysis of sulfur, the limit of the detectable content is only reached at five parts per trillion (5 ppb). "We are therefore also ideally equipped for the future when it comes to meeting even higher quality requirements for our products," says Frenzel.
About The Dow Chemical Company
For about 15 years, the globally active chemical group The Dow Chemical Company (Dow) has relied on the equipment of Analytik Jena GmbH. Founded in 1897, the company is one of the world's leading manufacturers of basic and specialty chemicals as well as high-performance materials. The US-American group based in Midland/Michigan is one of the ten largest US companies in Germany. Dow has also been present in the Central German region since 1995 and continues the traditional history of plastics and chemical production at its locations in Schkopau, Böhlen, Leuna and Teutschenthal.